Our Tube Forming Processes
At ETI we target difficult manufacturing opportunities that require engineering and ingenuity. Our proprietary equipment and processes allow for continuous tubular designs and provide our customers with superior solutions. We produce from ISO-9001 certified locations, and supply critical parts for diverse complex OEM applications.
We have over 50 years of experience as a leading company in custom tube fabrication and aluminum extrusions.
Material Capabilities
Stainless Steel
-
304L (Welded and Seamless)
-
316L (Welded and Seamless)
Copper Alloys
-
C12200 (DHP – Refrigeration – Stock)
-
C10100 (OFE)
-
C10200 (OFE)
-
C70600 (90/10 Copper–Nickel)
-
C71500 (70/30 Copper-Nickel)
-
C26000 (Yellow Brass)
Carbon Steel
-
J524 (Seamless Hydraulic)
-
J525 (Welded Hydraulic)
-
A179 (Seamless – heat – exchanger)
-
A214 (Welded – heat – exchanger)
-
A513 (Welded & DOM)
-
A519 (Seamless)
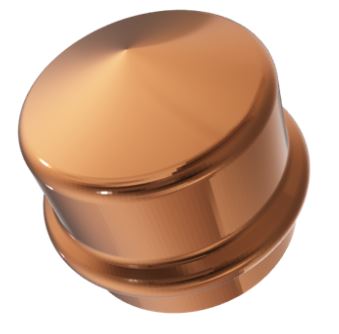
Spun Copper Press Caps
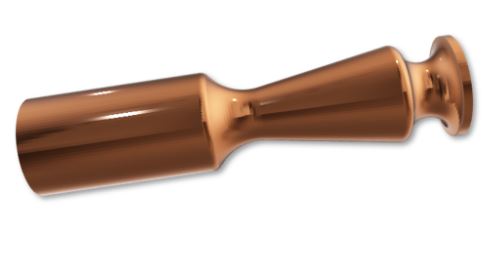
Spun Copper Lighting Applications
Fabrication Capabilities
-
Single Bending
-
Coiling
-
Forming
-
Multiple Bending
-
Cutting to Length
-
Flow Drilling
-
Brazing
-
Deburring
-
Milling
Tube-End Fabrication Capabilities
-
Bending
-
Chamfering
-
End Closing
-
Grooving
-
Beveling
-
Coping
-
Expanding
-
Swaging
-
Bificated / Multi-Ports
-
Deburring
-
Flaring